Cold Isostatic Pressing: A Revolutionary Manufacturing Process
Cold isostatic pressing (CIP) is a high-pressure forming process used to shape and densify materials under uniform pressure in a liquid or gas medium at room temperature. This advanced manufacturing technique has gained prominence across various industries due to its ability to produce complex geometries with exceptional density and mechanical properties. In this blog post, we’ll explore what cold isostatic pressing is, how it works, its applications, benefits, and why it’s transforming modern material processing.
---
●What Is Cold Isostatic Pressing?
Cold isostatic pressing is a method of compacting powdered materials into near-net shapes using hydrostatic pressure. Unlike traditional pressing methods that apply uniaxial or biaxial forces, CIP applies pressure equally in all directions, ensuring uniform compaction and minimizing defects such as cracking or warping. The process typically involves the following steps:
1. Material Preparation: Powders of metals, ceramics, composites, or polymers are prepared and loaded into flexible molds or encapsulated in rubber or polymer bags.
2. Pressure Application: The mold or bag is submerged in a liquid (usually water or oil) inside a pressure vessel, where hydraulic pressure is applied uniformly from all sides.
3. Compaction: The high pressure causes the particles to consolidate, achieving high green density before sintering or further processing.
Pressures used in CIP can range from 150 MPa (21,750 psi) to over 400 MPa (58,000 psi), depending on the material and desired properties.
---
Hydraulic Press
●How Does Cold Isostatic Pressing Work?
The core principle of CIP lies in the application of isostatic (equal) pressure. Here's a step-by-step breakdown:
1. Mold Design: A flexible mold or container is designed to match the desired component geometry. The mold is filled with the powdered material and sealed.
2. Loading: The sealed mold is placed inside a pressure chamber filled with a liquid medium, typically water or oil.
3. Pressurization: Hydraulic pumps generate high pressure within the chamber, transmitting it uniformly through the liquid to the mold. This pressure compresses the powder particles, causing them to pack tightly together.
4. Unloading: Once the desired pressure and holding time are achieved, the pressure is released, and the compacted part is removed for further processing.
---
●Applications of Cold Isostatic Pressing
CIP is widely used across industries due to its versatility and ability to produce components with superior properties. Some key applications include:
1. Metallurgy
- Producing near-net-shape parts for aerospace, automotive, and industrial sectors.
- Manufacturing tool steels, superalloys, and other high-performance materials.
2. Ceramics
- Creating dense ceramic components for electronics, medical devices, and cutting tools.
- Producing large or intricate shapes that would be difficult to achieve with traditional pressing methods.
3. Composites
- Compacting fiber-reinforced composites for lightweight structures in aerospace and defense.
- Forming hybrid materials with tailored mechanical and thermal properties.
4. Medical Devices
- Fabricating orthopedic implants, dental prosthetics, and other biomedical components requiring precise dimensions and biocompatibility.
5. Nuclear Industry
- Producing fuel pellets and structural components with high density and uniformity.
6. Energy Sector
- Manufacturing electrodes, electrolytes, and other components for batteries and fuel cells.
---
●Benefits of Cold Isostatic Pressing
1. Uniform Density
- CIP ensures consistent density throughout the part, reducing porosity and improving mechanical strength.
2. Complex Geometries
- The process allows for the creation of intricate shapes without the need for costly tooling or secondary machining.
3. High Precision
- Parts produced via CIP exhibit excellent dimensional accuracy and surface finish.
4. Material Versatility
- Suitable for a wide range of materials, including metals, ceramics, composites, and polymers.
5. Cost-Effectiveness
- Reduces material waste and minimizes the need for post-processing, lowering overall production costs.
6. Scalability
- CIP can be scaled up or down to accommodate small-batch prototyping or mass production.
---
●Challenges and Limitations
While CIP offers numerous advantages, there are some challenges to consider:
1. Equipment Costs: High initial investment in specialized equipment and infrastructure.
2. Cycle Time: Longer cycle times compared to conventional pressing methods, especially for large or thick components.
3. Material Constraints: Certain materials may require additional treatments or binders to achieve optimal results.
4. Post-Processing: Depending on the application, CIP parts may still require sintering, heat treatment, or machining to meet final specifications.
---
●Innovations in Cold Isostatic Pressing
Advancements in technology continue to enhance the capabilities of CIP:
1. Advanced Materials: Development of new powders and composites tailored for specific applications.
2. Automation: Integration of robotics and AI for improved efficiency and quality control.
3. Hybrid Processes: Combining CIP with additive manufacturing (3D printing) to create complex structures with enhanced properties.
4. Environmental Sustainability: Efforts to reduce energy consumption and recycle waste materials during the CIP process.
---
●The Future of Cold Isostatic Pressing
As industries increasingly focus on lightweight, high-performance materials and sustainable manufacturing practices, cold isostatic pressing is poised to play a critical role in shaping the future. Its ability to produce complex, high-density components with minimal waste makes it an ideal solution for emerging applications in aerospace, automotive, renewable energy, and healthcare.
Looking ahead, innovations in CIP technology will likely lead to faster production cycles, broader material compatibility, and even greater precision. These advancements will enable manufacturers to push the boundaries of what’s possible, driving innovation across multiple sectors.
---
●Conclusion
Cold isostatic pressing is a transformative manufacturing process that combines precision, versatility, and efficiency to deliver superior results. From producing cutting-edge aerospace components to fabricating life-saving medical devices, CIP continues to redefine the possibilities of modern material processing.
What do you think about the potential of cold isostatic pressing? Share your thoughts in the comments below! Together, let’s explore how this remarkable technology can shape a brighter, more sustainable future.
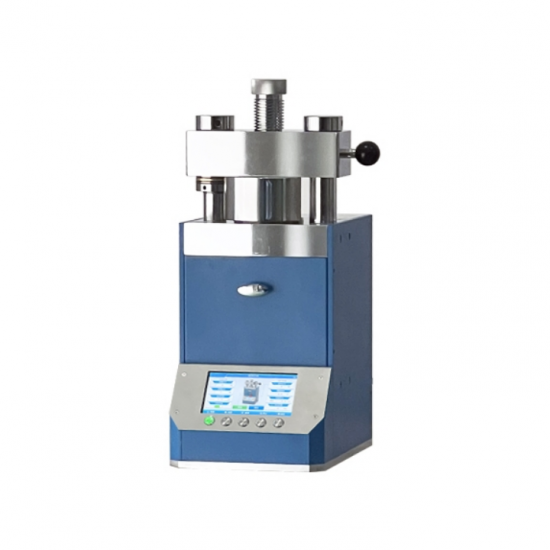